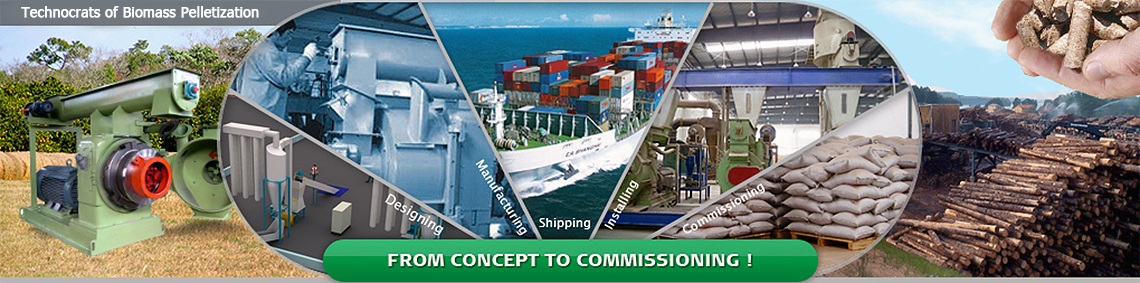
Make High Quality Wood Pellets with Pellet Plant
As an important alternative to fossil fuels, wood pellet fuel is being widely used for home heating and industrial production nowadays. The latest market research shows that biomass wood pellets are in great demand worldwide. Then, how to produce high quality wood pellets would be a key question for almost every wood pellets manufacturer. This post will give you a step-by-step guide on how to make high quality wood pellets.Raw Materials for Wood Pellets Production
The first thing you should consider once you have decided to build a biomass wood pellet plant, is where to build it. The answer will depend on the availability of raw materials. It is a good choice to put your plant in agricultural or forest areas. Adequate supply of raw materials can reduce the production cost and transportation cost.
There are many types of materials can be used to produce biomass wood pellets. Theoretically, almost any sort of vegetation can be compressed into pellets through a complete pellet plant. While in actual production, crop stalks and wood shavings are the two main widely used materials. For each sort of vegetation has its own features, it is flexible to choose different materials to meet the production needs.
Wood Pellets Production Steps
Wood pellets production is generally divided into 8 steps:
1. Raw Material Crushing
In the first step, raw materials need to be crushed into small pieces. Whether the raw materials are logs, corn stalks, grasses or other types of vegetations, they must be fragments with proper sizes to be pelletized by the pellet mill. If large size material is directly put into a pellet mill, it would block the circle of die and rollers. There are many types of crushing equipments, you can choose wood chipper or wood waste shredder according to the different characteristics of the materials.
2. Material Drying
During the process of pellet production, the moisture content of materials is an important factor that straightly affects the quality of the wood pellets. Proved by practical cases, the optimum moisture content of raw materials is from 10% to 15%. Either too high or too low moisture content would result pellet forming failure. If the material’s moisture content is above 20%, it must be dried by a dryer or mixed with other dry materials before being pelletized. In the same way, it’s also important to keep the moisture content of finished wood pellets in a low level. Wood pellets with high moisture content would generate more smoke when burning, which will affect directly the combustion efficiency.
3. Initial Sieving
The third step is screen, separate impurity from the raw materials. Because the materials are gathered from forestry waste and crop stalks, they are inevitably mixed with contaminants like metal objects, stones and other foreign materials. In the process of initial sieving, bigger substances like gravel can be picked away manually; ferrous metals can be separated by magnets covered on the surface of conveying belt. In some large-scale pellet plants, magnetic separators are widely used to sieve the materials. The using of magnetic separators can save labors and improve efficiency.
4. Grinding
The next step is grinding the materials in a hammer mill. The hammer mill has a rotating shaft with free-swing hammers attached to it. When it is working, the materials inside would be broken apart until they are small enough to fall through a screen with openings corresponding to the desired particle size. Besides the grinding process, the mixing of the materials is also completed here. In the hammer mills, the materials could be mixed evenly, thereby realizing the high combustion efficiency of wood pellets. It has been proved that the high efficiency of hammer mills depends on the coordination of every part, including appropriate hammer patterns, well-sized screens, and well-designed air. So regular maintenance is the key to make the process stable and smooth.
5. Pelletizing
Pelletizing is the core step in the wood pellets production. After being grinded, the materials will be fed into a pellet mill. Under the compression of the pellet die and roller, materials would be squeezed through the die holes and shaped into pellets. In this step, additives are often used for better binding and lubrication, the use of additives can also decrease the possibility of combustion problems.
6. Pellet Cooling
The fresh made wood pellets are very hot and soft. It’s necessary to cool and dry them before packaging. The easiest way to cool the pellet is spreading them out in the open air.
7. Final Sieving
During the pelletizing process, some material may failed to be compressed into pellets because of lacking pressure or lacking binder. These material is referred to as fines. The percentage of fines depends on the performance of the pellet mill and the quality of finished wood pellets. Pellets should be sieved before packaging. The fines can be recycled to the production line. Pellets with fewer fines would be more popular with customers because of their good looking and high quality.
8. Wood Pellet Pack and Store
Normally, wood pellets may not be used for fuel immediately after they were produced. In order to keep the wood pellets dry, the packing process is necessary. To improve work efficiency and reduce the cost, it is better to equip the pellet plant with a pellet packing machine. And the packed pellets should be stored in the dry and cooling place with good ventilation, and the pellets should avoid hot sunshine.